5 La “Calchera” (800 m s.l.m.)
Come veniva prodotta la calce
Le fornaci per la produzione della calce erano un tempo molto importanti per l’edilizia locale e rappresentavano un piccolo reddito aggiuntivo per i valligiani, in quanto i materiali impiegati erano facilmente reperibili in loco. La pietra da calce veniva agevolmente recuperata dai detriti di falda e frana che contornano alla base le pareti delle Pale o lungo il letto del Tegnàs. Il combustibile, costituito da grosse fascine di rami di latifoglie (faggio, nocciolo, frassino, carpino), era in parte lo scarto della legna da ardere e di quella utilizzata nelle carbonaie.
Calchera o fornace di calce costruita con conci di dolomia.
Breve storia della calce
La calce è un prodotto che l’uomo ha iniziato ad usare molti millenni fa. Una datazione precisa non esiste ma si può presumere grazie al ritrovamento a Mallaha (Palestina) di una abitazione con le pareti intonacate a calce e dipinte di ocra rossa risalente a circa 14-15 mila anni fa. La diffusione dell’uso della calce iniziò tra il 7000 e il 6000 a.C. in Mesopotamia e in Anatolia. Nella penisola balcanica arrivò attorno al 5600 a. C.. La conoscenza del processo di decarbonatazione, idratazione e ricarbonatazione era già uniformemente diffusa più di 2000 anni prima di Cristo, periodo in cui comparvero i primi forni verticali ritrovati in Mesopotamia, molto simili a quelli moderni.
Si ritiene che quasi tutti i popoli antichi come gli Egizi, i Cinesi, i Maya, i Fenici, i Greci e i Romani abbiano conosciuto la tecnica della cottura della calce ed il suo uso. Furono i Romani però a perfezionarla e ad impiegarla diffusamente. Infatti il primo trattato dettagliato e completo sulle malte a base di calce è il De Architectura di Marco Vitruvio Pollione del I^ secolo a.C.
La cottura della calce avviene all’interno di strutture (fornaci o forni) chiamate nelle nostre zone calchere. Si distinguono vari tipi di forni le cui caratteristiche variano a seconda della qualità del prodotto finale che si vuole ottenere.
Le prime fornaci da calce utilizzate erano concepite con caratteristiche semplici:
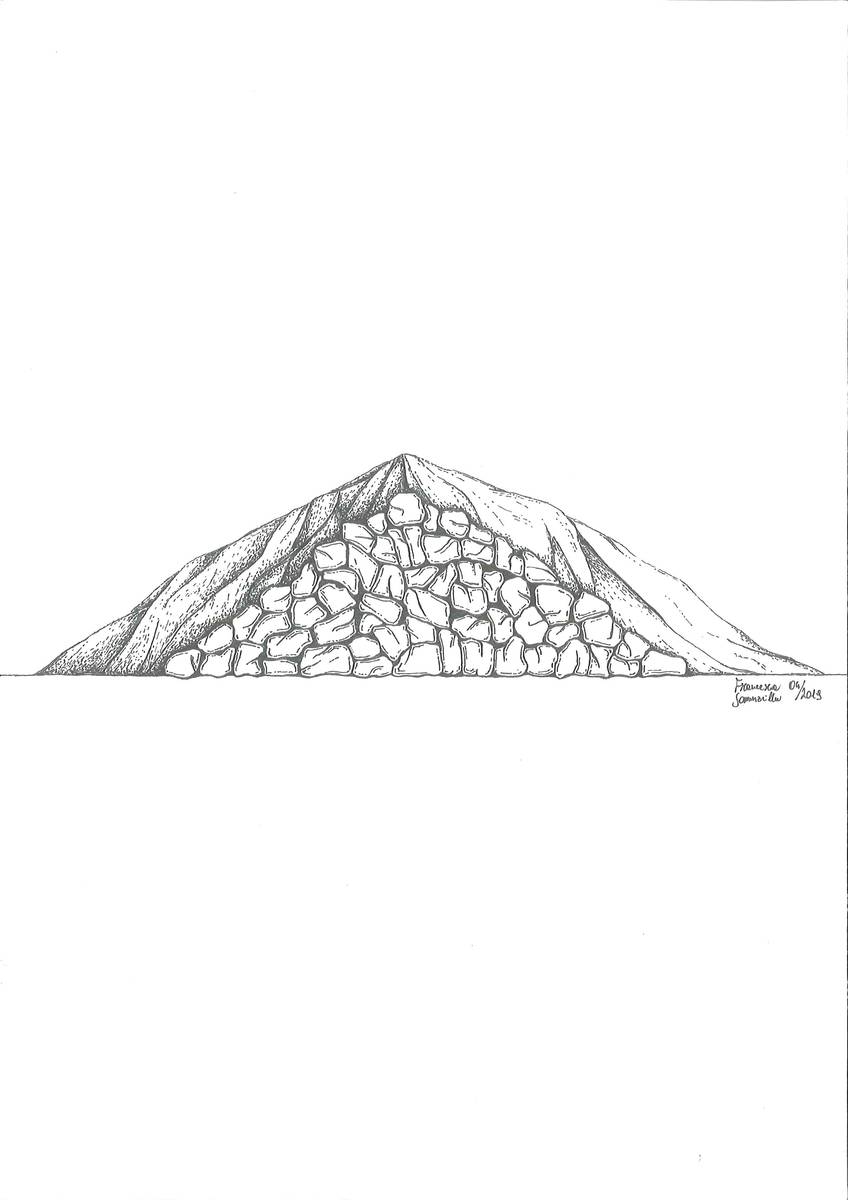
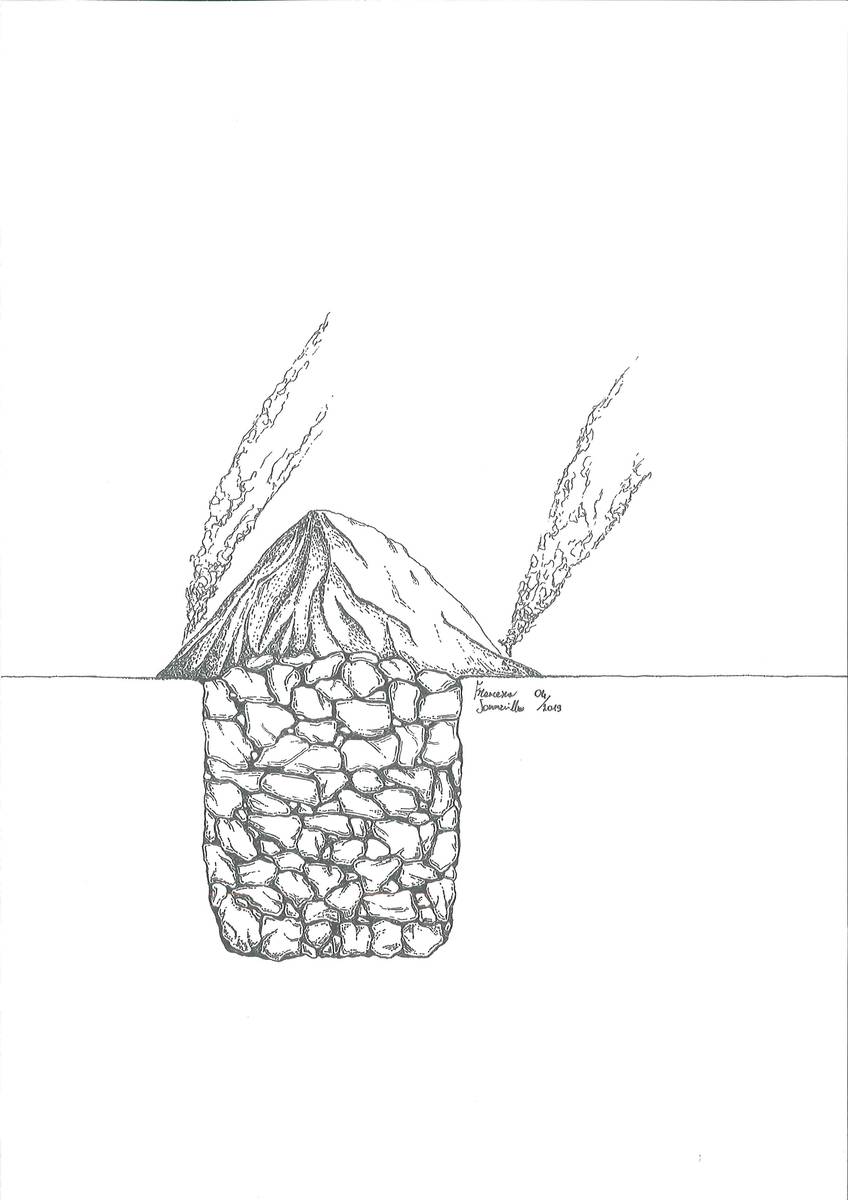
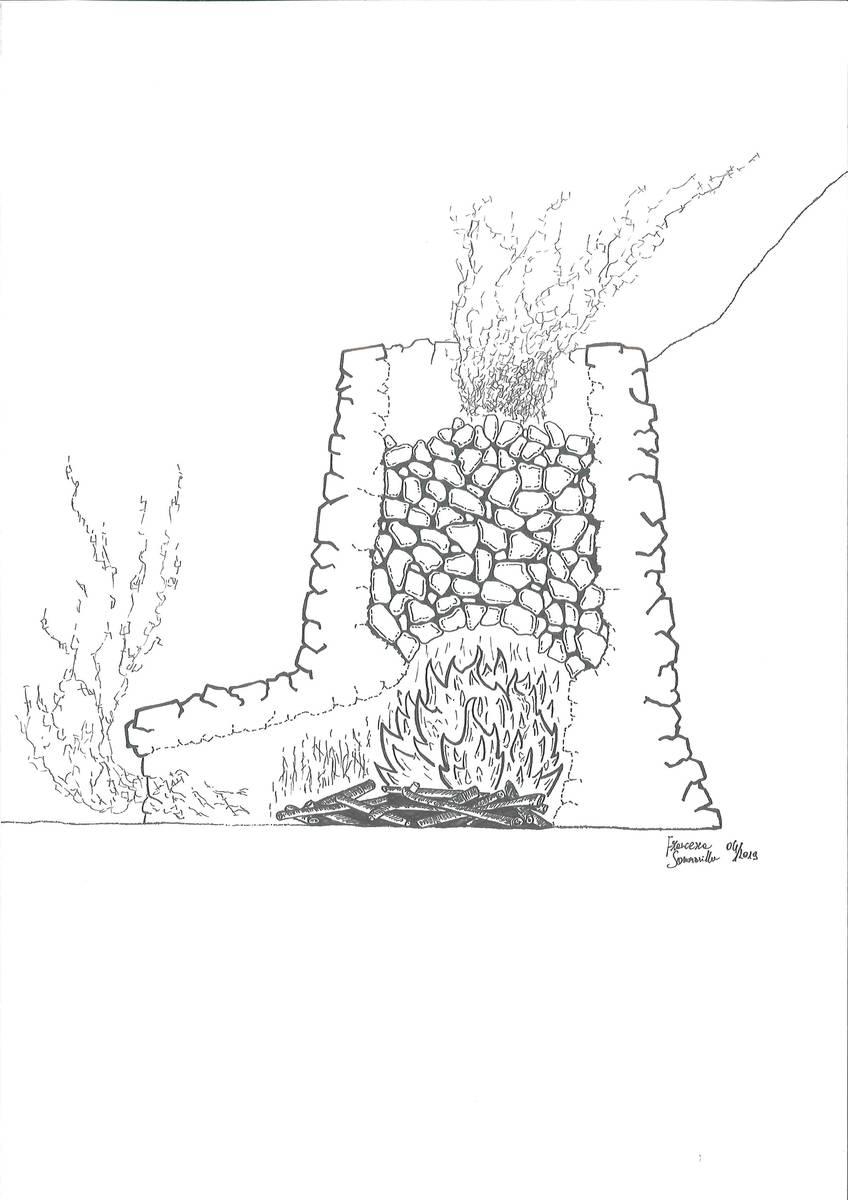
-fornace a catasta: su una superficie piana venivano accumulate pietre carbonatiche poi ricoperte con legna secca, raccolta nei boschi e sterco. Essi venivano incendiati e il fuoco veniva mantenuto sino al termine della cottura.
-fornace a fossa: veniva scavata una buca (preferibilmente in un terreno argilloso perché questo con il calore induriva assicurando una tenuta termica) che veniva riempita con pietre carbonatiche, si ricopriva il tutto con il combustibile che veniva incendiato e alimentato sino al termine della cottura.
In seguito le conoscenze acquisite promossero uno sviluppo tecnologico che portò alle fornaci in muratura utilizzate fino a qualche decennio fa nelle nostre zone e ancora visibili nei territori dolomitici. Le fornaci venivano costruite nei fianchi dei pendii in modo tale che, escludendo la parte frontale della fornace, fossero completamente interrate per poter evitare il più possibile la dispersione del calore. La costruzione avveniva scavando una fossa circolare nel fianco di un pendio, essa veniva rivestita internamente con pietre a secco resistenti alla cottura, lasciando nella parte anteriore inferiore un foro di accesso da utilizzare per alimentare il fuoco.
I tre tipi di fornaci elencati sono detti a fuoco intermittente. In questo tipo di fornaci le pietre non sono a diretto contatto con il combustibile ma sono solo lambite dal calore, motivo per cui il prodotto finale è costituito da calce bianca, pura, di ottima qualità, perché calcinata uniformemente.
Le fornaci a fuoco continuo prevedevano l’alternanza di strati di calcare con strati di combustibile e il prodotto che ne derivava era di qualità indubbiamente inferiore perché inquinato dai residui del combustibile.
Nel XIX secolo con l’avvento dell’industrializzazione nacquero i primi grandi forni ad imbuto a caricamento continuo con il combustibile che non veniva mai a contatto con il materiale trattato ottenendo così della calce priva di inquinanti.
Costruzione e uso della “calchera” agordina.
Per la costruzione della “calchera” veniva praticato uno scasso, generalmente di forma circolare, nel pendio individuato, di grandezza variabile in base alla quantità di calcare o dolomia che si intendeva trattare, quindi si rivestiva l’interno con sassi a secco che dovevano resistere alla cottura (sass rosp). Sulla parte bassa anteriore si lasciava un’apertura di grandezza variabile tra il metro e il metro e cinquanta attraverso la quale veniva caricato il combustibile. Il muro della fornace era più spesso alla base in modo da ottenere una rientranza di circa 20-25 cm ad una altezza dal fondo di circa 40-50 cm nella parete interna, realizzando così un gradino sul quale si appoggiavano i blocchi di calcare o dolomia predisposti a cupola autoportante sorretta da una intelaiatura provvisoria in legno per facilitare la costruzione dell’arco portante. Questi conci servivano a reggere durante la cottura tutto l’altro materiale dello stesso tipo gettato caoticamente all’interno della fornace. I blocchi utilizzati aveva una pezzatura variabile, ma tale da creare degli spazi tra una pietra e l’altra in modo da permettere il passaggio del calore. Una volta caricata l’intera fornace si costruiva al di sopra una piccola tettoia per impedire in caso di pioggia lo spegnimento della stessa. Quindi si procedeva all’accensione usando ramaglie e in seguito si continuava ad alimentare con ramaglie o legna di pezzatura fine in modo che il fuoco fosse sempre vivo e mantenesse una temperatura di circa 1000 C° necessaria per il processo di decarbonatazione. La quantità di legna occorrente per la produzione della calce poteva variare in base alla grandezza della fornace: per quelle più comuni, del diametro di circa 3 m e circa e di pari altezza, si poteva quantificare tra i 70 e gli 80 kg per quintale di calce prodotta. Naturalmente anche la durata della cottura variava in base alla grandezza, per quelle delle dimensioni da noi citate era in media di circa una settimana.
La calce viva prodotta al termine della cottura veniva posta in cassoni e idratata ottenendo così il grassello di calce come prodotto finale, che in genere veniva fatto riposare e maturare in apposite buche per mesi prima di essere utilizzato.
Il processo chimico
La calce aerea si ottiene per cottura (calcinazione) di calcari o dolomie a alta temperatura fra i 900 e i 1200 °C. Il calcare, carbonato di calcio (CaCO3), a 900 °C si trasforma in ossido di calcio (CaO) detto calce viva, con liberazione di CO2. L’ossido di calcio ottenuto ha la proprietà di trasformarsi facilmente in idrossido di calcio [Ca(OH)2] per aggiunta di acqua. In seguito a questa reazione fortemente esotermica, detta spegnimento, si forma una pasta morbida e molto plastica detta "grassello". L'indurimento, che da principio è una semplice essicazione (presa), prosegue poi come fenomeno chimico, una lentissima trasformazione dell'idrato di calcio [Ca(OH)2] che combinandosi con il biossido di carbonio (CO2) dell’aria ritorna carbonato di calcio (CaCO3), raggiungendo così una coesione rilevante secondo la reazione:
Ca (OH)2 + CO2 -» Ca CO3 + H2O
La Dolomia (CaMg(CO3)2) si dissocia completamente a temperature comprese tra i 940 °C e i 1230° C secondo la reazione:
Ca Mg (CO3)2 -» CaO + MgO + 2CO2
Per fabbricare calce aerea buona (o "grassa") occorre calcare abbastanza puro. La presenza dell'ossido di magnesio (MgO) ha effetti diversi a seconda della sua concentrazione: a bassa concentrazione (calcari dolomitici) rende "magre" le calci, ad alta concentrazione (dolomie) si hanno ancora calci "grasse".
La calce prodotta partendo dalla dolomia presenta, su tempi brevi, una resistenza maggiore di quella calcarea, ma su tempi molto lunghi nascono alcuni problemi, perché, per interazione con l’atmosfera si formano efflorescenze di solfato di magnesio che la deteriorano.
Download
![]() |
Scarica l'intero contenuto del pannello informativo n.5 (formato pdf) |